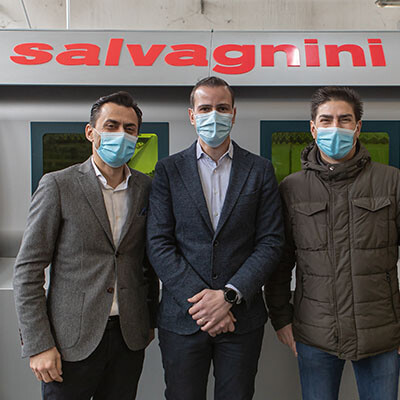
Case study
Biquadro: solving problems with digitalization
In a market ruled by the function “lower quantities, shorter times, lower prices”, developing a production chain based on a balanced ratio of output, price and quality has become a tough challenge. Which Alessandro Boni and Gian Rodolfo Brutti, owners of Biquadro, have taken up and are winning, thanks to their high-performance production systems, as they embrace the increasingly digital future of sheet metalworking.
Solving problems with digitalization
Highlights
- Biquadro
Biquadro S.r.l. has two hearts: its sheet metal division, which works as a sheet metal job shop, and the marine division, which designs and manufactures steel components for the naval and yachting worlds. Around 70% of the turnover comes from the sheet metal world, with a customer base working in various sectors: from electronics to industrial automation, from the production of building materials to generators, from compressors to HVAC. - The background
The S4 punching-shearing machine and the P4 panel bender, Boni and Brutti’s first investment in 2007, are still working in the company. But Biquadro’s production layout has increased significantly, and the relationship with Salvagnini has become stronger and stronger. Between 2016 and 2019, to cope with the increasing production volumes, Biquadro bought and installed two laser systems, both Salvagnini, both equipped with a store-tower, ensuring full autonomy. - The project
Biquadro began its digital revolution by implementing a company ERP. The main objectives were to control production, calculate costs precisely, ensure traceability and share information. The project then continued with the implementation of OPS, the Salvagnini modular production management software. - The outcome
“OPS is a great help because, with a single interface, we are able to monitor everything we have to produce, what is nested and what has already been produced on all our machines,” says Gian Rodolfo, one of the two owners of Biquadro. “If one machine’s load is higher than that of the others, OPS allows us to transfer the jobs from one machine to the other, balancing production. OPS has also helped us to extend job lengths on the S4 punching machine, thus increasing its production autonomy: we used to create programs by item, by multiples, whereas today we group all the items together by material and thickness, and are able to run longer jobs; we also nest everything dynamically, which we couldn’t do before.”
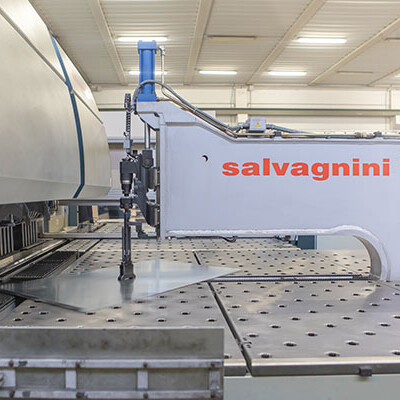