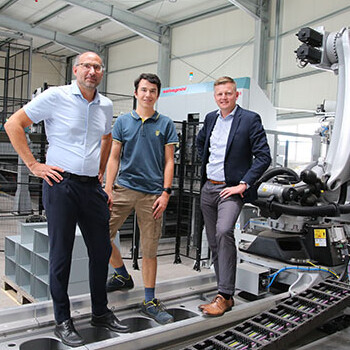
Case study
Erhart: highly-efficient kit production from batch-one
Story and pictures courtesy of N. Novotny/Blechtechnik
In order to maintain a constant high-quality level for the production of firefighter wardrobes and wall hydrant cabinets and remain cost-efficient regardless of the aggressive price competition above all from Eastern Europe and Asia, Erhart GmbH has invested in a Salvagnini S4 + P4 production line. Thanks to the new production system, the components are automatically punched, bent and then stacked by a robot, and the company's capacity considerably increased.
Highly-efficient kit production from batch-one
Highlights
- Erhart
Erhart GmbH has been producing wall hydrant cabinets for more than 50 years. It's the last Austrian manufacturer in this industry. The company also specialises in firefighter wardrobes, sold under the well-known name of Wagner Garderoben. - The context
In the last few years, it has become increasingly clear that it would have been impossible for Erhart to meet production targets due to low staff numbers and a shortage of machinery. - The project
After constructing a new hall, Erhart decided to invest in new machinery and choose a Salvagnini S4+P4 production line. The whole process, including punching, bending, and robotic stacking of sheet metal components, is now totally automated. - The outcome
Thanks to Salvagnini's S4+P4 line in use since December 2021, Erhart can now manufacture batch-one, make-to-order products in a very flexible, fast, and simple manner. With the complete elimination of the setup times and part handling between the machines, Erhart sped up production times by at least 40% while reducing energy consumption by 55%.
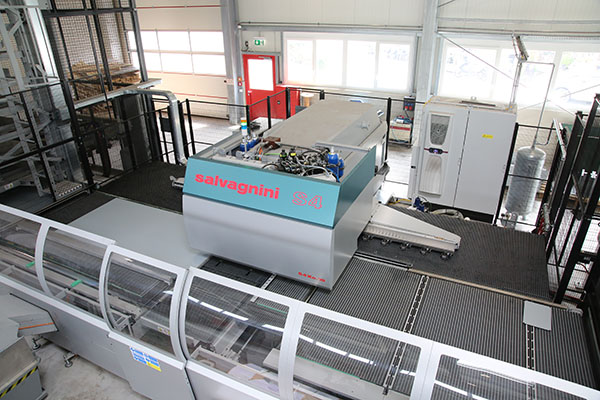
Check out the case study
Hear what Andreas Chiocchetti, Managing Director at Erhart, says about this project.