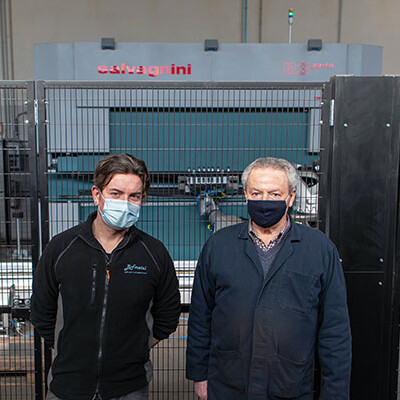
Case study
BF Metal: a passion for automation
What convinces a company with over 50 years of experience in sheet metal working to innovate? Or again: which technological, strategic or other issues drive them to invest in cutting-edge automated systems? We spoke with Andrea Boselli, owner of BF Metal, the company from Volta Mantovana (MN) which in 2019 purchased a Salvagnini ROBOformER robotic bending cell with a wide range of options, including devices for automatic tool change and set-up.
A passion for automation
Highlights
- BF Metal
With two owners and eight employees, BF Metal S.n.c. is a job shop, working particularly for the agricultural and automotive industries. 50% of machining work is done on zinc-coated sheet metal up to 5 mm, 40% on pickled sheet metal from 1 to 25 mm thick, while the remaining 10% of material processed is aluminum and stainless steel. - The context
Automation began to revolutionize work at BF Metal with a store-tower with loading/unloading device that served the Salvagnini L3 laser purchased in 2016. "It was the perfect choice, 100%: it has allowed us to extend working time and regain autonomy, especially at night, when the laser can work unmanned," says Andrea Boselli, owner of BF Metal along with his father. - The project
“In 2018 we recorded significant growth: lots of orders, from both the automotive and the agricultural sectors,” Boselli recalls. “We could have bought 2 or 3 more press brakes, but this meant more staff, which unfortunately are hard to find. And this is the context in which the idea of automating bending came about. But we didn't know what solution best met our needs: what was better, a panel bender or a robotic bending cell? And so we asked for Salvagnini’s advice again. We realized that a robotic bending cell was the ideal solution for us. I paid close attention to the AU-TO automatic tool changer, and we invested in a completely automated, full-optional system.” - The outcome
"Despite the work-loads, today we are extremely precise and reliable in terms of delivery time, and certainly more accurate than in the past. ROBOformER has allowed us to increase our quality: it ensures consistent bending quality. 300 parts are always 300 good parts: it is a highly repetitive machine. Our company has obtained IATF16949:16 certification, which requires the production of only good parts, and obviously here ROBOformER offers all its support with its precision. Another huge advantage we are happy with is in the process: in 2020 we produced a total of over 800,000 parts. Some of our items are produced in thousands of units a month, and completing them requires 2 or 3 traditional bending machines to be set up. ROBOformER makes the parts autonomously, without reworkings. The AU-TO tool changer easily manages this variability: there are no more down times, and is much quicker than manual re-tooling. Even if we re-tool several times a day, the time savings compared to a manual press brake are clear. And ROBOformER has brought another huge advantage: higher productivity. A bit like the laser loading/unloading store-tower, which has allowed us to regain autonomy by working unmanned, and extend working times. It would be practically impossible to go back," Boselli concludes.
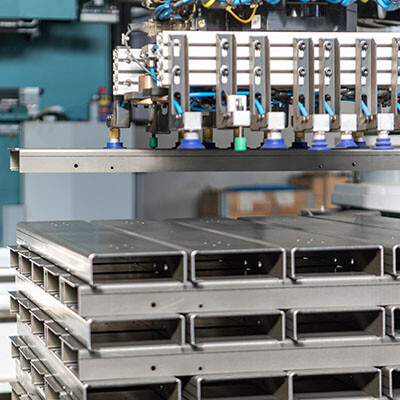