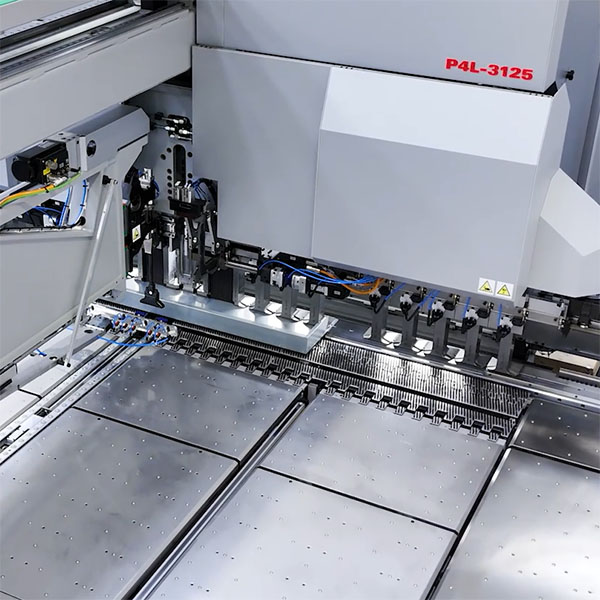
Insight
Tecnolaser: Rethinks service to cut production time by 40%
Rethinks is Salvagnini's service to help companies take on the day-to-day challenges imposed by the market by rethinking and redesigning their production to get the most from their systems.
Rethinks is a service exclusively for Salvagnini customers to help them exploit the potential of their systems for an even higher competitive position in the market. Rethinks connects customers with skilled Salvagnini specialists to optimize production process and improve quality and efficiency, reducing the number of work steps, material usage and costs. Rethinks includes two service options: a design course for designers and a part design support service.
The first option is a customized design course for designers. The goal is to work upstream to improve the knowledge of the specific technologies at the production site, enabling more efficient use of them. The design course provides designers with advanced skills.
The second is a design support service. The Salvagnini specialists place their own experience and skills at the disposal of the customer's designers, helping them to design or redesign their products. This is real expert support for the operational steps of component design, identifying the best solutions for each case to guarantee reduced waste and the optimization of the whole production process, even upstream and downstream of the Salvagnini technologies.
Tecnolaser chose Rethinks
Giulio De Bardi, Board Member at Tecnolaser, explains the benefits achieved by using the Rethinks service for the redesign of machine covers.
- What sparked the idea to redesign the product?
"We often manufacture machine covers made of panels of various shapes and sizes. The production process that we implemented in-house consisted of laser cutting the panels then bending them in the panel bender which is versatile in making different sizes of the inner bending radius and then welding, a process we needed to close the panel angle and restore the aesthetic finish. Our critical issue was that this process took a lot of the operator’s time, thus saturating production capacity. However, the continuous welding and sanding processes required special skills from the operator and therefore we had the criticality that not all the staff at our disposal could perform this work in a precise and satisfactory way for the customer. Clearly, all this manual activity also results in high costs for the finished product we sell to our customers." - What's changed?
"We have modified the cutting section in terms of laser cutting. So, while before we had an edge which was then bent into the side bend that generated a 90-degree angle, we managed to obtain a small sheet metal lip which is bent with the radius bend and provides a visible support that gives continuity to the bending radius, while on the other hand the welding operation has become much simpler, allowing spot welding, no longer requiring sanding and also requiring less operator skills." - What are the benefits?
"This new solution has allowed us to reduce welding times. We managed to save 40% in the process, which in the average of our production is 15% of the cost of the finished panel. In addition, we now have the advantage that special manual skills are no longer needed by the operator in finishing the panel, grinding and reconstructing the bending radius. So, all our welders are now able to work the panels and perform the required productions."