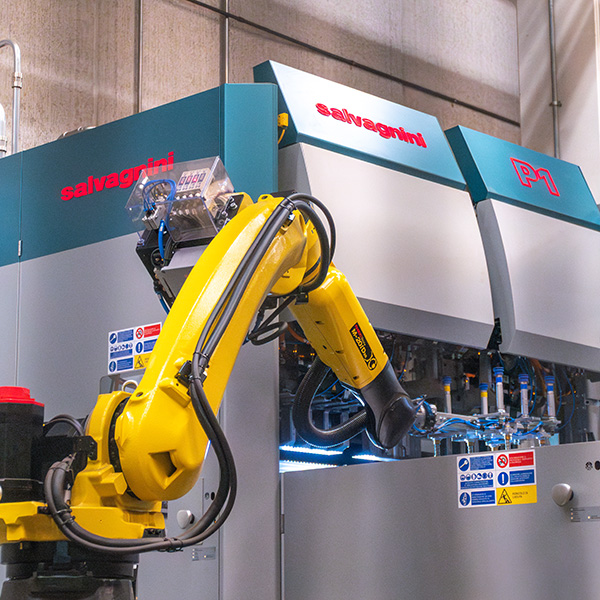
White paper
Robotics as a lever to address market challenges
In an era of increasing market challenges, automation is no longer just an option—it is a necessity. Robotics is playing a key role in transforming production processes, enhancing efficiency, and ensuring flexibility in response to growing customization demands and shrinking lead times. This article explores how Salvagnini’s innovative P-Robot is redefining the market, showcasing its potential through the case studies of Muraro Isidoro e Figli and Ricana Concept.
Automation, now more than ever, is an essential response to the challenges faced by the manufacturing sector in an increasingly competitive and dynamic market. Flexibility and efficiency have become critical priorities to manage smaller production batches, a growing variety of products, and short lead times. It is no longer merely a technological solution but a strategic lever capable of transforming production by combining advanced technology with human expertise to achieve superior results.
Yet automation is more than just technology. It is a paradigm shift that challenges old prejudices, demonstrating how the cooperation between humans and machines can reduce physical strain, improve safety, and enhance the value of human work. In this context, Salvagnini stands out for its innovative vision of flexible automation. The Group’s philosophy goes beyond optimizing individual production steps, aiming to create an integrated and intelligent production ecosystem that can adapt rapidly to market changes. Salvagnini’s solutions not only reduce setup times and waste but also eliminate low-value-added activities, enhancing quality and overall efficiency while creating a safer, more productive, and engaging work environment for employees.
Robotics represents perhaps the ultimate expression of automation, a natural evolution that integrates technology and intelligence to transform production processes. This is likely why the adoption of industrial robots has seen impressive growth in recent years, becoming one of the pillars of innovation in the manufacturing sector. Recent studies show that the number of operational robots globally has reached record levels, reflecting a steady increase in installations.
Industrial robots improve efficiency across all operational steps. They do more than replace human intervention in repetitive tasks—they integrate technologies that ensure greater precision and continuity, even in unmanned environments. Their ability to autonomously manage operations like material loading and unloading, assembly, and the processing of diverse components allows businesses to meet increasingly fragmented and specific production needs while freeing personnel to focus on strategic and creative activities.
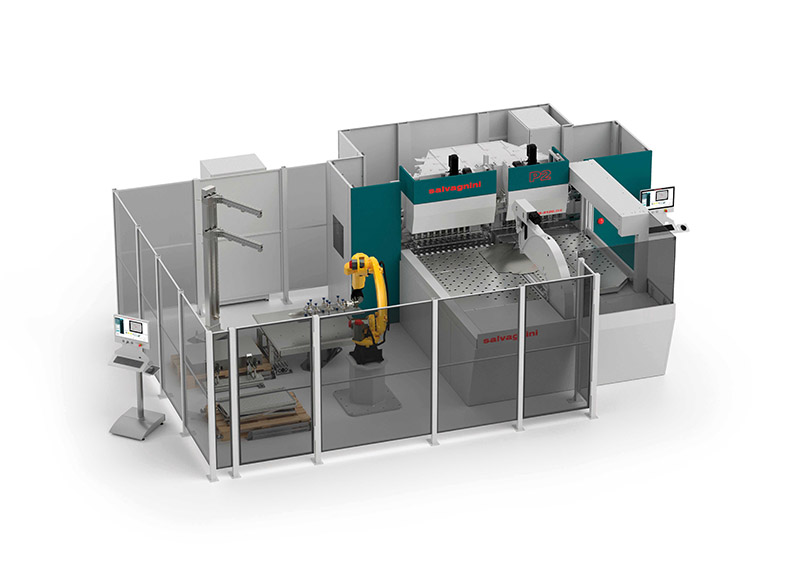
P-Robot: robotizing has never been this simple
It is in this context that Salvagnini introduced P-Robot, the application which combines a panel bender with a robot to produce kits, batches and single parts. P-Robot is a smart solution, much simpler than those already on the market: it is easy to program and use, and is able to exponentially improve the flexibility and productivity of the panel bender.
The P-Robot configuration can be customized: Salvagnini proposes simple production flows, with loading/unloading assistance only, and more complex systems including, for instance, automatic pallet handling or third-party integrations such as work centers for corner forming, labeling, laser marking, riveting and welding.
The flippable gripping device adapts automatically to the size of the part being handled. It is equipped with suction cups on both sides used to pick the finished part from the worktable of the panel bender, and in masked time, replace it with a new part to be bent. All this helps to optimize the sheet metal loading/unloading times, improve the production rate and substantial reduction in idle times.
P-Robot is used to choose the most suitable strategy for current production needs. On unmanned shifts, or in production contexts where a single operator monitors numerous systems, P-Robot naturally works in R2R (robot to robot) mode, loading, unloading and, if necessary, stacking the parts. But this is not an exclusive strategy: the same P-Robot can work in different modes, seamlessly and without re-tooling. In R2H (robot to human) mode, it is responsible solely for loading the flat part, whereas the operator is responsible for unloading the panel. This is an advantageous strategy if the operator must complete the processing of the panel on a different workstation – for example with a press brake or a welding machine. In H2R (human to robot) mode, it is the operator who will load the flat part onto the working area, and the robot will unload the panel at the end of the cycle: this strategy is useful for managing extremely diversified batch-one productions. Without forgetting that the panel bender nevertheless remains available for any work managed completely by the operator.
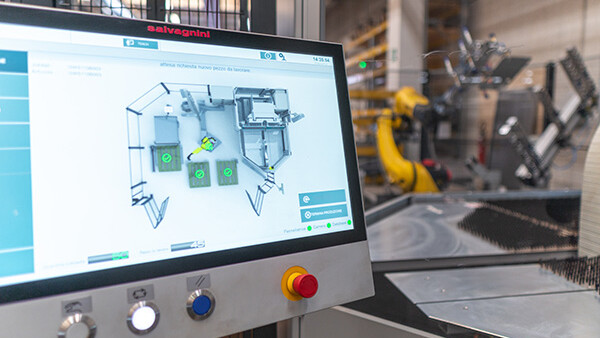
The panel bending program is done with STREAMBEND and can be used without the need for changes on both the P-Robot and on the standard panel benders. On board the machine, the MOVE software receives the panel bending program, generates the dimensions of the flat part and the finished panel and uses it to automatically generate the robot trajectories. MOVE also manages the intermediate robot movements independently, and the operator is only required to make a reduced set of movements: it is an authentic smart teaching system, that makes offline robot programming pointless.
And with the integration of the RVS option, an artificial vision system unique on the market, P-Robot recognizes and processes the parts fully autonomously. With cameras and sensors, the artificial vision device acquires an image of the surrounding environment and interprets it using artificial intelligence. RVS recognizes the parts, distinguishes the single sheets, and identifies the position of pallets and stacks without references. All this information is shared in real time with the panel bender and the robot, which adapt autonomously to ensure that the sheet metal is handled and positioned precisely.
It is natural to wonder how P-Robot is applied in real production scenarios. What problems can it solve, and what benefits does it offer to companies that choose to adopt it? To answer these questions, we examine two case studies where P-Robot has been successfully integrated into different production contexts, demonstrating its flexibility and strategic impact.
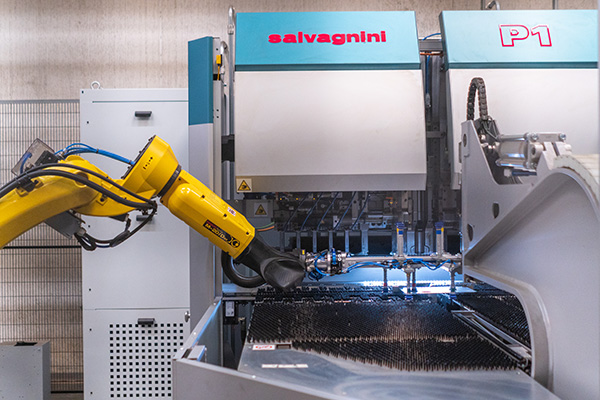
Integrating P-Robot into an established production workflow: Muraro Isidoro e Figli case study
At Muraro Isidoro e Figli, a subcontractor based in Brendola (Italy) with a long-standing focus on innovation, the introduction of P-Robot has proven to be a strategic step toward enhancing efficiency by optimizing production rates and drastically reducing setup times. The P-Robot installed at Muraro features an electric P1 panel bender with a consumption of less than 3kW and a compact layout.
“We already have other Salvagnini machines in our workshop,” explains Luca Muraro, “and we were able to speed up the commissioning of the new system. We hit the ground running, there wasn’t even time to stop, study, and learn. We simply transferred programs from one panel bender to another, adjusting the parameters according to the technical specifications of each machine. Today, we can switch production very quickly; for instance, while bending panel A, during the lunch break we can launch the production of a panel B. We had another robotized system that was far less flexible and required over two hours of setup to start production. Now, we can manufacture a simple component in five minutes, and a more complex one in just a few minutes more. In half a day, we completed a new production of 300 pieces, programming 1,200 bends from scratch. P-Robot extends production beyond traditional manned shifts, allowing operators to focus only on high-value-added tasks.”
Retrofitting to optimize productivity: Ricana Concept case study
Ricana Concept, based in Hillerstorp (Sweden), specializes in the production of shop fittings and display racks and is recognized as a market leader in this sector. With over 30 years of experience and a dynamic team, Ricana Concept offers both standard and customized solutions to its customers. Its focus on innovation and efficiency has led the company to consistently invest in automation, transforming traditional processes into modern, technologically advanced workflows.
The installation of a fully automated Salvagnini laser significantly increased Ricana Concept’s production capacity but created a new challenge. “When we purchased the L5,” explains Johan Petersson, CEO of Hestra Inredningar AB, Ricana Concept’s mother company, “our capacity increased so much that, despite having a panel bender, bending became a bottleneck. We decided to robotize our Salvagnini P2 by adding a robot to ensure a bending process that was just as efficient. P-Robot solved this issue, delivering improved production efficiency and better ergonomics for operators.”
For Ricana Concept, retrofitting the panel bender allowed the company to optimize its existing system, enhancing overall efficiency with a more cost-effective investment.
Do you have any questions?