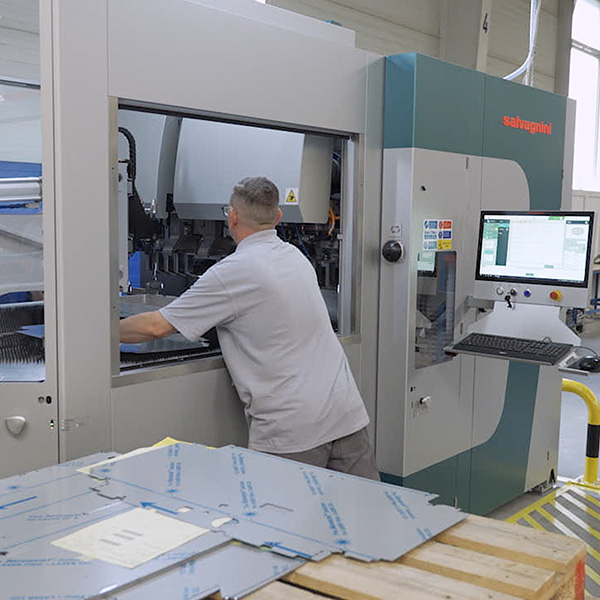
Case study
Krosno Metal: panel bender after panel bender, towards continuous improvement
Krosno Metal sp. z o.o. has reduced production costs per unit, implemented lean manufacturing principles, reduced tool changeover time, shortened order fulfillment time, increased efficiency, and optimized labor costs thanks to continuous investments in new technologies, and in particular thanks to the recent purchase of a Salvagnini P1 panel bender.
Panel bender after panel bender, towards continuous improvement
Highlights
- Krosno Metal
Krosno Metal sp. z o.o., better known as Rilling, its trade name, is a leading manufacturer of professional refrigeration equipment for the HO.RE.CA. industry with a product range that includes refrigerated and freezer cabinets, refrigerated and freezer tables, refrigerated bar counters, waste coolers and highly advanced high-speed blast chillers. Modern manufacturing and continuous improvement of production processes, delivery times that do not exceed 48 hours, and respect for the environment are the key pillars for its good positioning and the high customer satisfaction. - The context
Krosno Metal production has always relied on Salvagnini panel benders. The company came into contact with Salvagnini in 2010, when it purchased its first panel bender, a semi-automatic P4. In 2014, Krosno Metal introduced in the machinery fleet the panel bender that best suited to its manufacturing needs, a P2 panel bender with a maximum bending length of 2.5 meters. - The project
In 2022 Krosno Metal chose again Salvagnini as a partner, opting for the fully electric P1 panel bender, which consumes less than 3 kilowatts of energy and has a footprint of just 8 m2. “We chose the P1 to produce items with a maximum bending length of 1,250 mm and sheet thickness of 1.3 mm”, says Marcin Pawlak, the Technical Manager. - The outcome
“The P1 is the perfect machine for producing many of our stainless steel items. With the P1 we were able to relieve the workload on the P2 while maintaining the same product quality and speed of operation. Moreover, we now work in two shifts without overtime, even with 3 extra hours. In conclusion then, there were many benefits: the reduction of production costs per unit, the implementation of lean manufacturing principles, the reduction of tool changeover times, the increase in efficiency, the reduction of order processing times and the optimization of labor costs,” ends Pawlak.
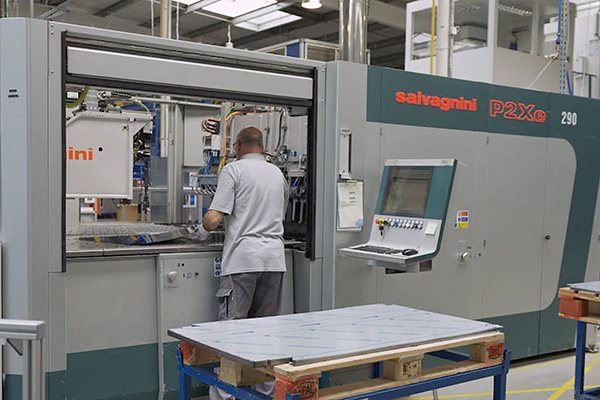
Check out the case study
Hear what Krosno Metal executive team says about Salvagnini machinery.