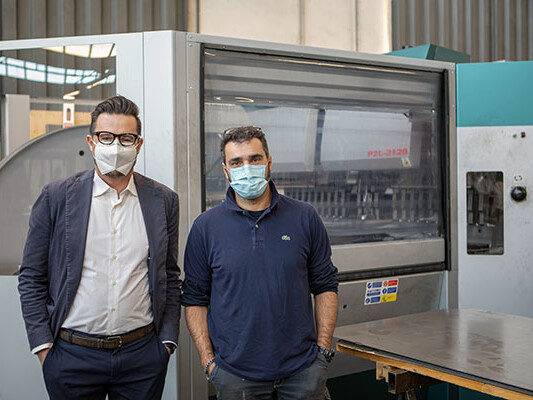
Case study
Metalsystem: the panel bender is a fundamental step to grow
Metalsystem has been processing sheet metal for its customers for decades. Over time this family-run company has grown, both in terms of staffing and in technical terms, with the introduction of new process automation technologies. We met Fabio Pollastri – the owner, with his sister, of Metalsystem – to talk about the company’s latest investment: a Salvagnini P2 panel bender, installed very recently.
The panel bender is a fundamental step to grow
Highlights
- Metalsystem
Metalsystem has a large and well-balanced market: from food processing to automotive, and from air treatment to refrigeration. The strong point of this Modena-based company is also its ability to provide clients with a service, covering all the main sheet metal component machining jobs: with a consolidated network of partners, Metalsystem can provide cutting, bending, welding, painting and external treatments. All in all, this is an advanced subcontractor. - New projects...
“Two years ago we launched a new project to produce air conditioners,” Pollastri explains. “90% of sheet metal components are panels. Cutting wasn't a problem, but the bending department was under pressure: the panels are large, heavy and awkward to handle. This meant having two operators working on a traditional press brake. Without even considering the re-tooling time, calculated in hours. There are 15 of us, and I couldn’t devote two staff just to that production: I had to decide how to automate the process.” - ...new opportunities
The solution chosen by Metalsystem is a P2-2120, one of the most successful models in the Salvagnini panel bender range. “I would never have been able to consider another solution,” Pollastri goes on. “I am 100% satisfied with the investment, because it’s exactly what we needed: while on average we produced a batch of 40/50 conditioners in 20 days, today we produce a batch of 200 parts in 10 days.”
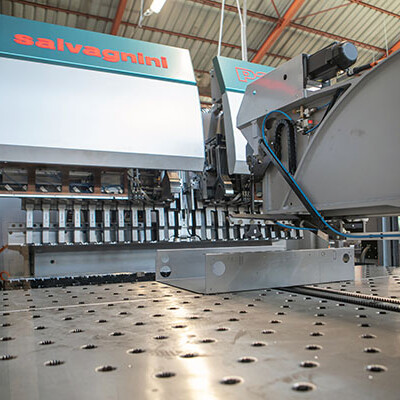