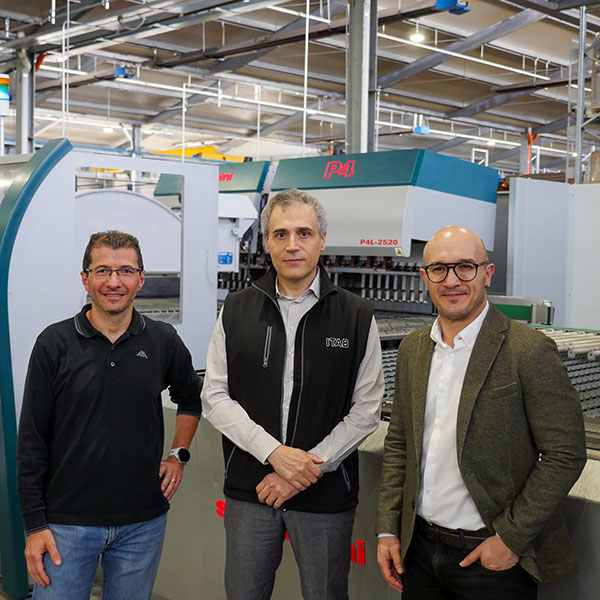
Case study
ITAB: innovation and global growth in the production of sheet metal shelving
Story courtesy of F. Chiavieri/L’Ammonitore
ITAB, one of the largest international groups of companies specialized in retail concepts, checkouts, lighting systems, shop furniture, and equipment has invested in a new automated Salvagnini S4+P4 line, achieving significant benefits in terms of product customization, flexibility, reduced energy costs and lower energy consumption.
Innovation and global growth in the production of sheet metal shelving
Highlights
- ITAB
ITAB ITALY was founded under the name La Fortezza S.p.A in 1962 in Scarperia (FI), as a manufacturer of metal shelving/racking, later becoming part of the Swedish listed multinational group ITAB. ITAB ITALY manufactures checkouts and shelving for shops and supermarkets. It exports the majority of its production to the Middle East, France, Spain and Eastern Europe, as well as supplying an Intercompany market which includes the other group companies. - The context
In an ever-more dynamic and demanding market, investing in sustainability can mean significantly improving a company's profit, influencing operating costs linked to productivity, energy consumption, flexibility and much more. Automation of production processes can make a significant contribution to business sustainability. ITAB ITALY began investing in innovative technologies over 20 years ago, identifying Salvagnini as its technology partner for the installation of flexible production systems. The latest investment involves a new Salvagnini S4+P4 line purchased in 2022 which entered production in autumn of the same year. - The project
The S4+P4 line chosen by ITAB ITALY is composed of an MBT dual store-tower, S4 punching machine, MC sorting and stacking device, RIP turnover unit, and P4 panel bender. A first point of interest is indeed the store, which allows the punching machine to be fed with single sheets to manage the jobs fully automatically, depending on the job-list and its priorities. The S4 punching-shearing machine can process sheets measuring up to 3048x1650 mm, while the P4 panel bender – in 2520 configuration – is able to bend panels with maximum length of 2500 mm. Between these two machines there is an MC automatic sorting device and an RIP turnover unit. The new Salvagnini line works manned over three shifts, from Monday to Friday. Thanks to the integration of industry 4.0 technologies, the line is fed with single sheets via backflushing, as production gradually progresses, allowing to systematically and fully track, manage, and record the use of raw material in a completely automatic way, also improving productivity and reducing stock. - The outcome
“Thanks to the installation of this new line,” explains Luca Banchi, VP of Operations at ITAB, "we solved some clear issues with the previous system, first and foremost the maintenance costs for the hydraulic components. In confirmation of the validity of the investment, many of these costs are now essentially zero. Our new line makes use of advanced hybrid technology to significantly reduce consumption: a solution which improves our sustainability. We have obviously calculated ROI against a wide range of parameters: reductions in maintenance costs and energy consumption, but also a reduction in the manual operations to complete our production cycle. All this translates into a lower total cost for the finished product. According to our estimates, a well-industrialized product on this line, compared to purchasing from a subcontractor responsible for the laser cutting, bending, welding etc. costs around 35% less”.
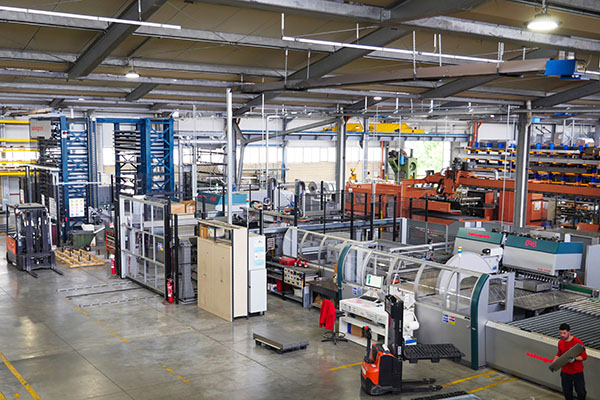