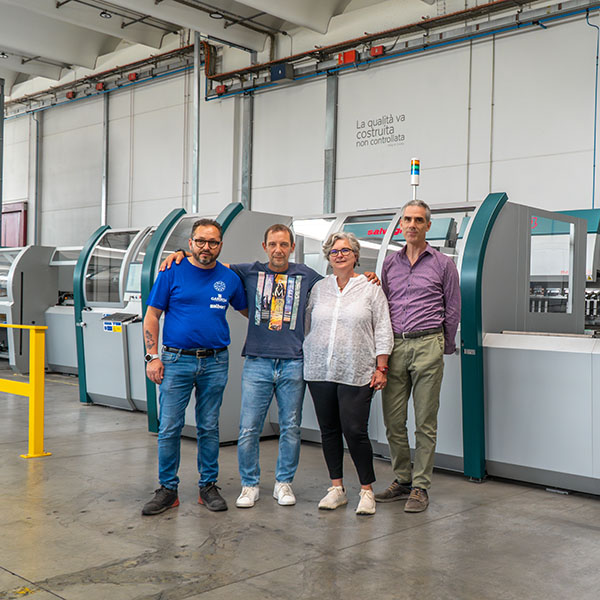
Case study
Gardesa: cutting-edge technology and maximum efficiency
Story courtesy of D. Davò, M. Bonaria Mereu, F. Della Muzia/Tecnolamiera
Speed, optimization, and flexibility in manufacturing are just some of the numerous benefits which have led Gardesa to purchase and profitably operate systems manufactured by Salvagnini for years, just as the new S4+P4 line installed in its plant, combining a punching-shearing machine with an automatic panel bender.
Cutting-edge technology and maximum efficiency
Highlights
- Gardesa
It was way back in 1979 when six people with various experiences founded Gardesa in Cortemaggiore near Piacenza in northern Italy, which produced industrial doors, before moving on to the manufacture of security doors. To date, the company sells its products both in Italy and abroad; at home, the main customers are resellers, costruction warehouses, hardware stores, and construction firms, with a dedicated line for retailers. Abroad, Gardesa operates primarily in China and Europe. - The context
The relationship with Salvagnini has been in place for nearly 30 years: the first punching machine arrived in 1998, followed immediately afterwards by a panel bender. January 2022 saw the installation of the new line completed; this consists of an S4 punching-shearing machine and P4 panel bender in 3216 configuration, with the first press brake also installed. In September 2023, the second B3 was installed. - The project
Gardesa's new S4+P4 line is fed by two MD single sheet store-towers, ideal for just-in-time production of kits or batch-ones, with 30 trays which ensure high levels of line autonomy and flexibility for single-sheet processing. The S4 maximizes process efficiency because all the feeding, punching, forming, separation and unloading operations are automatic, done by a single system that eliminates semi-finished parts, does not require manual intervention and assures extreme repeatability. Fed completely automatically by the punching machine, the P4 panel bender natively combines productivity, with its automatic bending/handling cycles, and flexibility, with its universal bending tools. The model chosen by Gardesa allows a maximum bending length of 3200 mm to be achieved, with a maximum height of 165 mm. Although the line is completely automated, its use is simple and intuitive thanks to FACE, Salvagnini’s HMI. As regards the specifics of the security door product notes that this is highly variable but parameterizable, in that many similar items are produced, but which are installed in contexts in which the height and width vary. Choosing a parametric production system was essential to be able to handle very large quantities. - The outcome
“In the terms of the goal achieved, one of the benefits of this new punching machine/panel bender line is undoubtedly the speed of production and the increased material efficiency, because by optimizing the nesting we have reduced scrap. A key element for us, even on the basis of an extension of the range of products we were able to create, is the dual vertical store-tower, which allows us to manage up to 30 different material formats. This means not only reducing the ground footprint, but also greater order, with all materials under control”, explains Massimiliano Rossi, Head of Product Development and Feasibility.
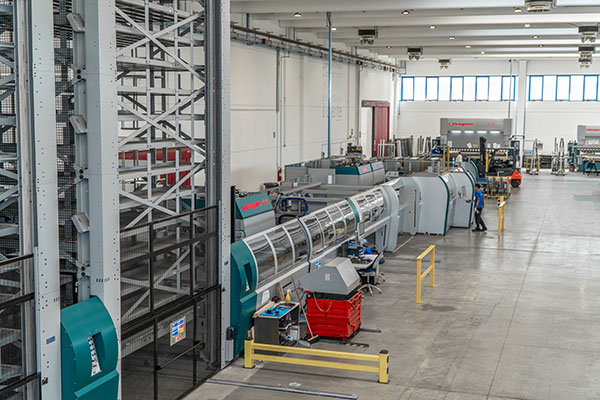