RVS (Robot Vision System) is an artificial vision system that automates the intermediate steps of recognition, handling and programming.
RVS eliminates the need for human intervention and drastically simplifies part identification operations, making the process faster and more intuitive, reducing the risk of errors and improving overall efficiency.
This solution increases productivity without compromising the quality of the finished part.
Thanks to its integration with P-Robot, RVS makes it possible to process parts in a completely autonomous manner, increasing operational flexibility and permitting the handling of components that have complex geometries or that cannot be centered with traditional gravity centering devices.
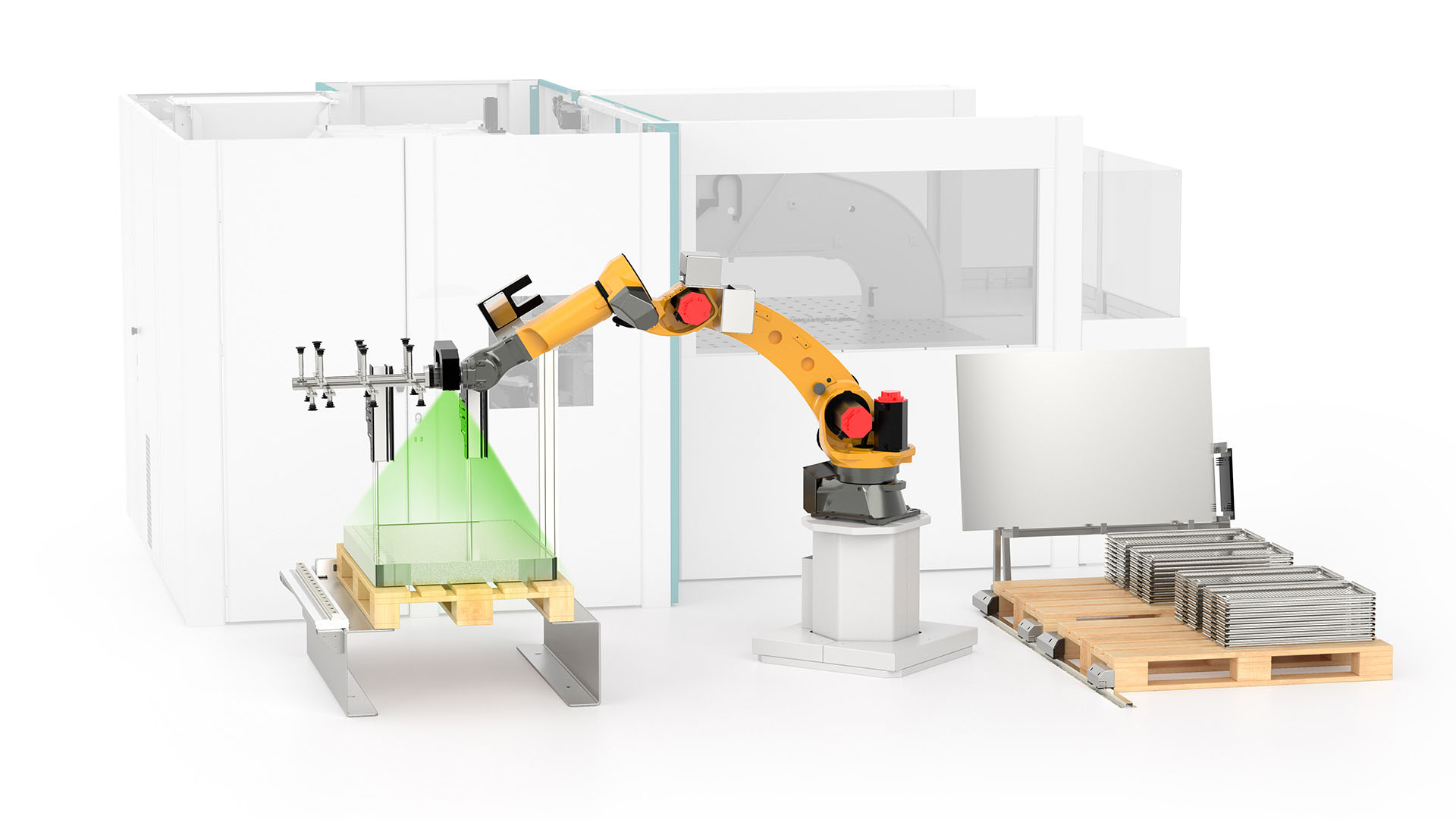
The system acquires an image of the surrounding environment and interprets it using artificial vision.
RVS is capable of:
- recognizing parts, even in unordered stacks;
- distinguishing individual metal sheets;
- identifying pallets and stacks without the need for physical references;
- sharing all information in real time with the panel bender and the robot, which adapt themselves automatically to guarantee precise handling and positioning.
- RVS scans the loading station, recognizes the geometry of the part, automatically associates the program and starts production until it is completed.
- It is ideal for unordered stacks of identical parts and drastically reduces the times for preparing the material to bend.
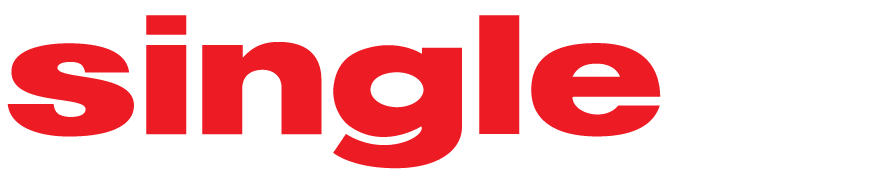
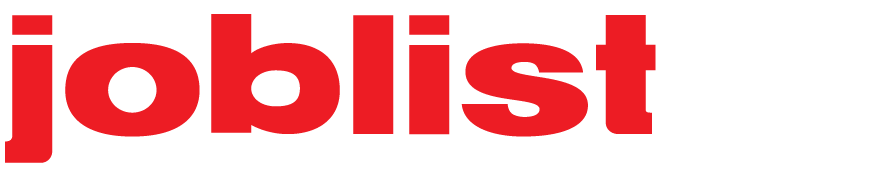
- RVS manages a predefined list of parts, recognizing them and picking them up in sequence, with simple positioning on the loading station.
- This is ideal for predetermined productions, in order to reduce the risk deriving from manual preparatory activities.
- RVS scans the loading station, automatically recognizes the parts and associates the program for each of them, producing the parts until they are depleted.
- Robot integrates with upstream systems, offering maximum flexibility.
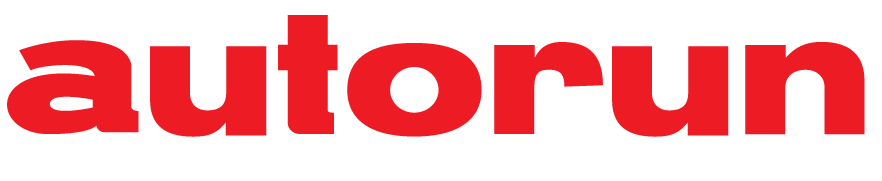
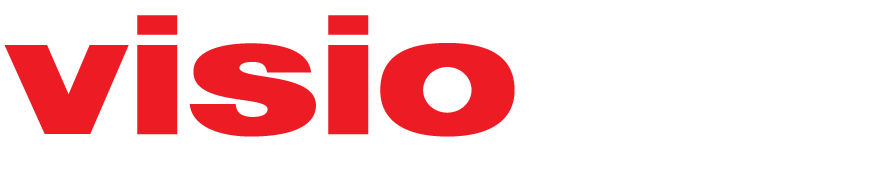
RVS offers a control option that verifies in real time the actual parts to be produced, rejecting the non-conforming ones.
The VISIO system compares the image acquired with the reference DXF, ensuring quality and reducing machine downtimes.
At the end of production, a report summarizes the checks that were performed.