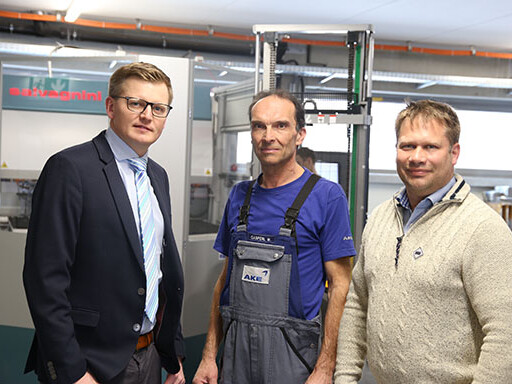
Case study
AKE: flexible, precise and highly productive
Story and pictures courtesy of N. Novotny/Blechtechnik
An automatic panel bender when specialist workers are in short supply: as part of the IDEAL AKE Group, AKE Ausseer Kälte- und Edelstahltechnik GmbH is a specialist in the custom design of refrigerated display cases from a batch-one order. In order to reduce the workload for specialist workers especially on press brakes, this company from Styria invested in Salvagnini’s P1 automatic panel bender about a year ago.
Flexible, precise and highly productive
Highlights
- AKE
The IDEAL AKE Group takes all of this into account for their refrigeration and heating devices, which can be found world-wide in the most prestigious restaurants, fast-food and supermarket chains. While IDEAL, with its plant in Gmunden (Upper Austria) has specialized in products for the kitchen industry, AKE, which is located in Kainisch (Styria) concentrates on the production of refrigerated display cases and products for the dispensing industry. - Reduced workload
Due to the massive shortage of skilled personnel, and in order to reduce the workload for the company’s bending specialists, AKE has for some time been playing with the idea of also investing in an automated bending solution. The time came in July of last year: the first Salvagnini P1 panel bender was put into operation at the AKE site in Ausseerland. Parts required in large batches can now be bent fully automatically with the new machinery solution without requiring skilled staff. - The output
The strengths of the P1 are particularly evident in the production of trays for refrigerated wells. When using conventional press brakes, the necessary bends had to be carried out in two work steps, which is quite time-consuming. The Salvagnini panel bender does this fully automatically in one production process and in a quarter of the time.
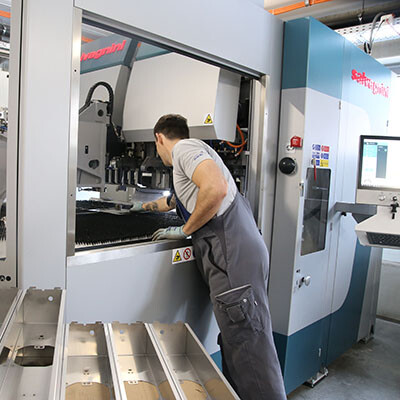
Check out the case study
Hear what Andreas Pilz, Technical Director at AKE, says about the P1 panel bender.