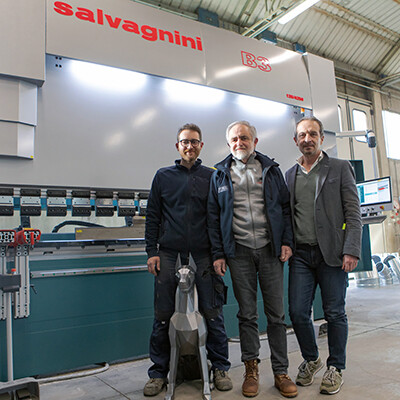
Case study
Aspir Mecc: all the advantages of a simple press brake
Since 1985, Aspir Mecc has been designing, producing and installing extraction systems for treating and purifying air of fumes, dust, solvents, exhaust gases and bacteria – pretty much everything that harms the environment and human health. To manage high variability in production, Aspir Mecc chose a Salvagnini B3 hybrid press brake.
All the advantages of a simple press brake
Highlights
- Aspir Mecc
With a staff of 9, including the owner, and a turnover that has grown over the years, Aspir Mecc works with small and medium businesses by supplying them with HVAC systems and a complete, customized service from design to installation and assistance. - The industry
Aspir Mecc built its niche in the world of wood processing machinery. The high level of customization affects the batch sizes and the production strategy: 4/6 panels per filter, plus the top and bottom, produced in kits and often in batch ones. - The project
The item turnover rate is quite high, and consequently so is the machine re-tooling frequency. Precisely to manage this variability in production, in 2020 Aspir Mecc chose a Salvagnini B3: a hybrid press brake with a maximum bending force of 135 tons and maximum bending length of 4250 mm, with 7 axes and 4 backgauges to ensure maximum flexibility in production. - The outcome
Today Aspir Mecc programs everything in the office: STREAMFORMER automatically proposes the ideal bending sequence. A side effect of programming in office is that it also helps to reduce the tool set-up time: the operators already know which punch is needed, and where it has to be positioned, so they avoid mistakes and wasted time.
