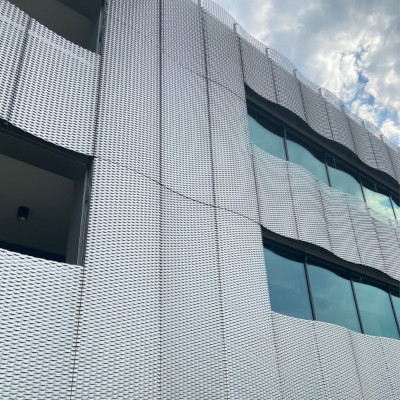
White paper
Sheet metal skins in the building industry: innovations, benefits, and production excellence
Sheet metal skins have become a vital element in modern building architecture, delivering not only aesthetic appeal but also enhanced performance in energy efficiency, durability, and sustainability. As the building industry focuses on innovative ways to design and retrofit facades, the use of metal skins has grown exponentially. Their versatility is particularly valuable for architects and engineers aiming to design dynamic, sustainable structures that meet the high standards of contemporary and future-oriented building codes.
The rise of sheet metal skins
The building skins market is booming, driven by the demand for durable, sustainable materials that enhance a building's energy efficiency. Sheet metal, often made from materials like aluminum, steel, or copper, provides exceptional flexibility and strength, allowing for complex designs and extended life spans. With increasing pressure on urban infrastructure and building codes shifting towards energy efficiency and environmental impact, sheet metal skins offer a practical solution to modern architectural challenges.
Market research predicts that the sheet metal skins industry will experience constant growth, primarily fueled by the demand for high-performance building facades and innovations in fabrication technology. The drive toward net-zero energy buildings and green architecture is a significant growth factor. Increasingly, architects and developers are choosing sheet metal skins not only for new buildings but also for retrofitting old structures to meet sustainability standards.
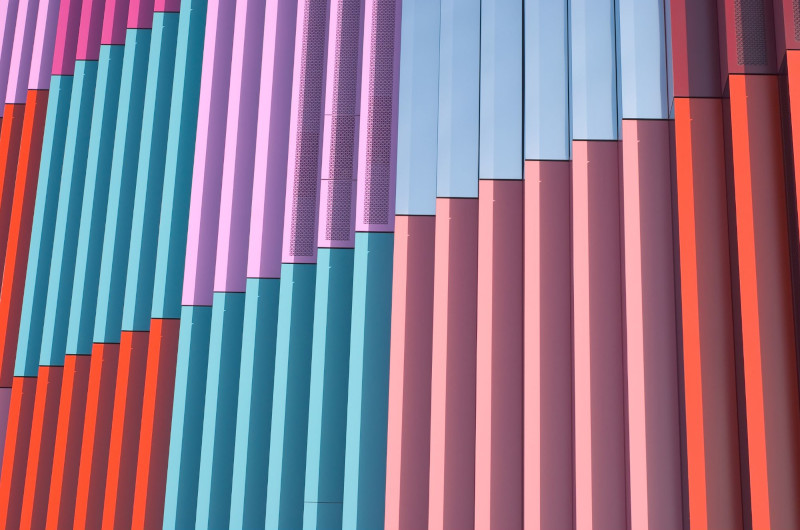
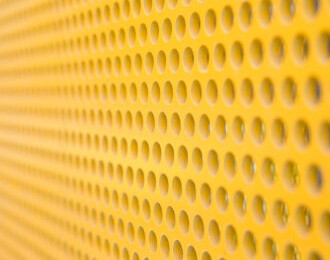
Benefits of sheet metal skins for public and private buildings
Sheet metal skins offer multiple advantages, from enhanced durability and maintenance efficiency to impressive energy performance. For both private residences and public structures, these skins can significantly improve operational costs by enhancing thermal efficiency, reducing energy needs for heating and cooling, and protecting the building from weather-related wear.
The versatility of sheet metal skins allows for a range of finishes, textures, and colors, adding character and identity to buildings while accommodating various architectural styles. From sleek, minimalistic facades to original, complex designs, sheet metal skins can be customized to meet a project’s unique requirements, giving architects substantial creative freedom.
Sustainability is a key advantage, as sheet metal skins can integrate solar panels and other renewable energy systems. In retrofitting projects, sheet metal skins offer an excellent method to enhance energy efficiency, often contributing to achieving certifications like LEED or BREEAM, which are increasingly vital in both commercial and residential industries.
The production process of sheet metal skins
The production of sheet metal skins involves multiple stages, including cutting, forming, bending, and coating. Among these steps, bending is critical, as it shapes the metal into forms that contribute both to the structural and aesthetic value of the finished facade. Precision in bending ensures that the skins fit seamlessly on the building’s framework, optimizing installation efficiency and structural integrity.
A standout feature of sheet metal skins is that they are typically custom products, designed specifically for each building to meet unique architectural and functional requirements. This customization satisfies a range of project demands, such as varying building dimensions, unique facade geometries, and specific aesthetic visions, making it essential to produce facades that can precisely fit these customized designs. Since no two buildings are identical, this level of customization is highly valuable, and Salvagnini panel benders are optimally suited to support this approach.
Bending in sheet metal skins production
Sheet metal bending is essential in defining the final shape and function of metal skins. Panel bending, in particular, is suited to complex geometric shapes, which are often required in facade designs. Salvagnini’s automated panel benders offer high precision and flexibility in sheet metal skin production, supporting both large series and batch-one production with customized designs. They handle individual, project-specific designs without requiring complex retooling or setup between different shapes and sizes. Salvagnini's parametric programming supports batch-one production and kit production seamlessly, which is especially advantageous for custom designs that require quick adaptation. Thanks to these machines' automatic adjustment systems, each panel can be tailored in real-time to meet precise measurements and specific design elements.
Adapting to millimeter precision without setup time
One of the biggest challenges in producing custom metal skins is adapting to specific, sometimes minute, dimensional requirements that might vary from panel to panel. For instance, fall-back or filler panels, which may be necessary to adapt a skin design precisely to a building’s dimensions, can be produced by Salvagnini panel benders without interrupting the production flow. Their zero setup time feature ensures that each panel—whether standard or a unique dimension—fits perfectly, maintaining consistent quality across the facade.
Salvagnini’s universal bending tools further streamline this process by accommodating different panel thicknesses and shapes without manual changes, reinforcing their role as the ideal choice for custom, high-quality sheet metal skins. This flexibility not only meets diverse architectural requirements but also ensures that each part is produced precisely, reliably, and efficiently, setting a new standard in custom facade production.
Streamlined production of interlocking, fixing, and stiffening systems
An essential aspect of high-quality sheet metal skins is their ability to integrate seamlessly into the structural framework of a building. Effective skin panels require precise interlocking, fixing, and stiffening systems that ensure durability and ease of installation, as well as resistance to environmental stressors. Salvagnini panel benders empower manufacturers to develop these critical systems directly within the bending process, reducing the need for secondary operations and optimizing both production and installation processes.
Traditionally, interlocking or fixing systems on metal skins might require post-production modifications, such as drilling, welding, or adding secondary structural elements. However, with Salvagnini’s advanced panel bending capabilities, these features can be integrated directly during the bending process. By enabling exact, programmable bends and geometries, Salvagnini machines allow manufacturers to create locking mechanisms, hooks, and additional stiffening panels as part of the main production run, minimizing the need for costly and time-intensive secondary modifications.
The precision and adaptability of Salvagnini panel benders result in skins that are easier to install on-site. With interlocking and fixing systems pre-fabricated into the panels, contractors can fit each panel accurately and safely onto the building’s framework without needing additional fasteners or supports. This streamlined approach reduces installation times, minimizes potential errors, and decreases labor costs, ultimately lowering the overall expense of the facade installation.
Furthermore, by adding stiffeners or ribs into the skins during the bending process, Salvagnini machines enhance the structural rigidity of each panel, ensuring that they maintain their form and alignment once installed. This capability not only improves the lifespan and durability of the panels but also reduces the likelihood of warping or movement over time, leading to a high-quality, low-maintenance facade solution.
Salvagnini’s unique combination of precision, efficiency, and flexibility is thus instrumental in creating sheet metal skins that are robust, installation-friendly, and cost-effective, aligning with the building industry’s increasing demand for streamlined, sustainable construction methods.
Salvagnini panel benders: enhancing flexibility and productivity in metal skin manufacturing
Salvagnini panel benders are renowned for their versatility, enabling manufacturers to execute complex bends with speed and precision. These panel benders are equipped with universal bending tools, eliminating the need for re-tooling, which drastically reduces downtime and enhances productivity. This is particularly valuable for sheet metal skin manufacturing, where the flexibility to produce different shapes and designs in quick succession is essential.
Key features of Salvagnini panel benders
- Productivity and speed: Salvagnini panel benders achieve up to 17 bends per minute, making them highly efficient for large-scale production.
- Automatic in-cycle adjustment: The machines’ universal tools adjust automatically during production, allowing for seamless transitions between different bend requirements without stopping for manual changes.
- Parametric programming: Salvagnini’s parametric programming capabilities facilitate rapid adjustments to part sizes and angles, enabling batch-one and kit production without any additional setup time.
- Adaptability to material variations: Advanced sensors and adaptive algorithms (MAC3.0 technology) ensure consistent quality by adjusting for material thickness and other variables, minimizing waste and error.
- Unmatched dimensional capabilities for great lengths: Salvagnini’s portfolio of panel benders includes models capable of handling panels up to 4 meters in length. Bending a 4-meter panel with precision by hand is considerably more challenging than a shorter panel; Salvagnini panel benders optimize this process, ensuring accuracy and reducing labor complexity in producing large facade panels. This feature is invaluable for the building skins industry, where precision on large panels is critical, and achieving such accuracy manually is challenging.
Future of sheet metal skins in building design
The future of sheet metal skins is closely tied to the trajectory of sustainable architecture and smart building technologies. As adaptive systems and materials continue to advance, sheet metal skins will likely become more integrated with renewable energy solutions, such as photovoltaic cells, and smart climate-control mechanisms.
Sheet metal skins have redefined modern architecture, contributing to both the sustainability and aesthetic appeal of buildings. With state-of-the-art production methods, especially in bending, these facades represent a synergy of form and function that meets today’s market demands. Salvagnini panel benders, offering unmatched flexibility, productivity, and precision, have become essential in producing the complex designs that define the modern urban landscape. As the industry grows, the integration of adaptive technologies like Salvagnini's MAC3.0 and the broader adoption of sustainable building practices promise a future where sheet metal skins continue to be at the forefront of architectural innovation.
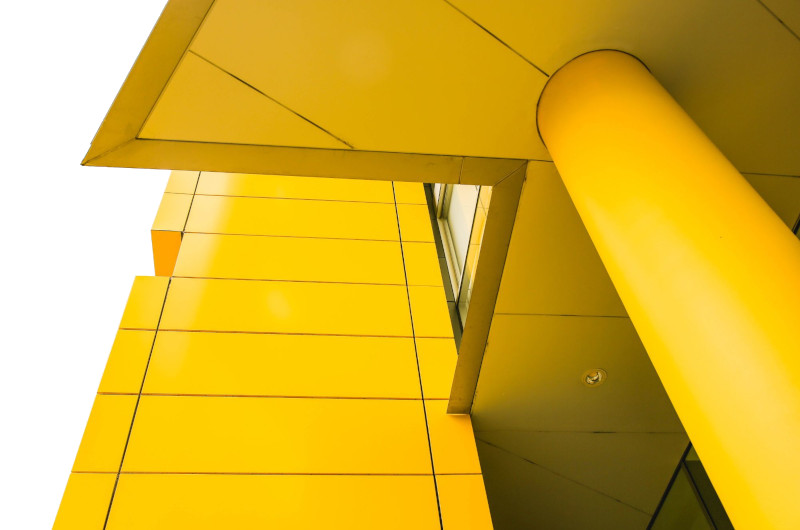
Do you have any questions?