판금 자동화 라인, 그 이상
중간 처리 없이 소재를 완전 자동으로 펀칭, 절단 및 절곡. 키트, 배치원 또는 연속 생산 등 모든 생산 전략에 이상적인 솔루션.
100% 유연 자동화
S4+P4 라인은 중간 처리 없이 소재를 완전 자동으로 펀칭, 절단 및 절곡합니다. 이 라인은 주문 생산 및 적시 생산, 생산 능력 및 속도 향상, 리드 타임 단축, 툴 교체 없이 다양한 소재 가공, 인력 활동 최적화 등의 이점을 제공합니다.
제품 개요
통합된 적응형 기술을 통해 S4는 지능적으로 다양한 변화에 자동으로 적응할 수 있어 낭비와 수정을 없애는 동시에 뛰어난 가공 품질을 보장합니다:
- 중심 조정 제어 시스템이 유입되는 소재를 측정하고 필요한 경우 실제 측정된 치수에 맞춰 프로그램을 조정합니다.
- 매니퓰레이터는 소재의 크기와 중량에 따라 설정을 변경하며, 가공되는 소재의 비율에 따라 핀서를 조정합니다.
- 자동 시스템이 매니퓰레이터 축의 열 팽창을 점검하고 변동 사항을 보정하여 뛰어난 위치 정밀도를 보장합니다.
- 샤링기는 간격을 자동으로 기록하며, 소재와 두께에 따라 필요한 힘을 적절히 조절합니다.
보관 및 자동 로딩/언로딩 장치는 시스템의 자율성을 향상시키며, 개별 가공 단계와 생산 공정 전반에 걸쳐 효율성을 높여줍니다. 또한, 광범위한 솔루션으로 매우 다양한 생산 전략에 대응할 수 있으므로, 실질적으로 모든 레이아웃 또는 구성 조건을 충족합니다.
S4 펀칭-샤링 복합기는 공정 효율성을 극대화합니다. 모든 로딩, 펀칭, 성형, 분리 및 언로딩 작업이 하나의 시스템에서 자동으로 실행되므로, 반제품이 생기지 않고, 수동 개입이 필요 없으며, 뛰어난 반복성을 보장합니다.
P4는 범용 절곡 툴(Universal Bending Tool)적용으로 장비를 멈추거나 수동으로 툴을 교체할 필요가 없습니다. 제품의 기하학적 형상에 따라 자동으로 툴이 조정되어 키트 생산 및 낱개흐름생산 모두 가능합니다.
첨단 센서, 벤딩 포뮬러, MAC 3.0 의 적응형 기술을 내장한 이 자동절곡기는 소재와 외부 환경의 변화에 자동으로 적응하도록 설계 되었습니다. 따라서, 소재 낭비와 수정 작업 없이 광범위한 제품의 생산이 가능합니다.
P4는 특수한 제품 형상 또는 다양한 로딩/언로딩 솔루션을 위한 보조 도구 및 추가 장치를 포함한 맞춤형 솔루션을 제공합니다.
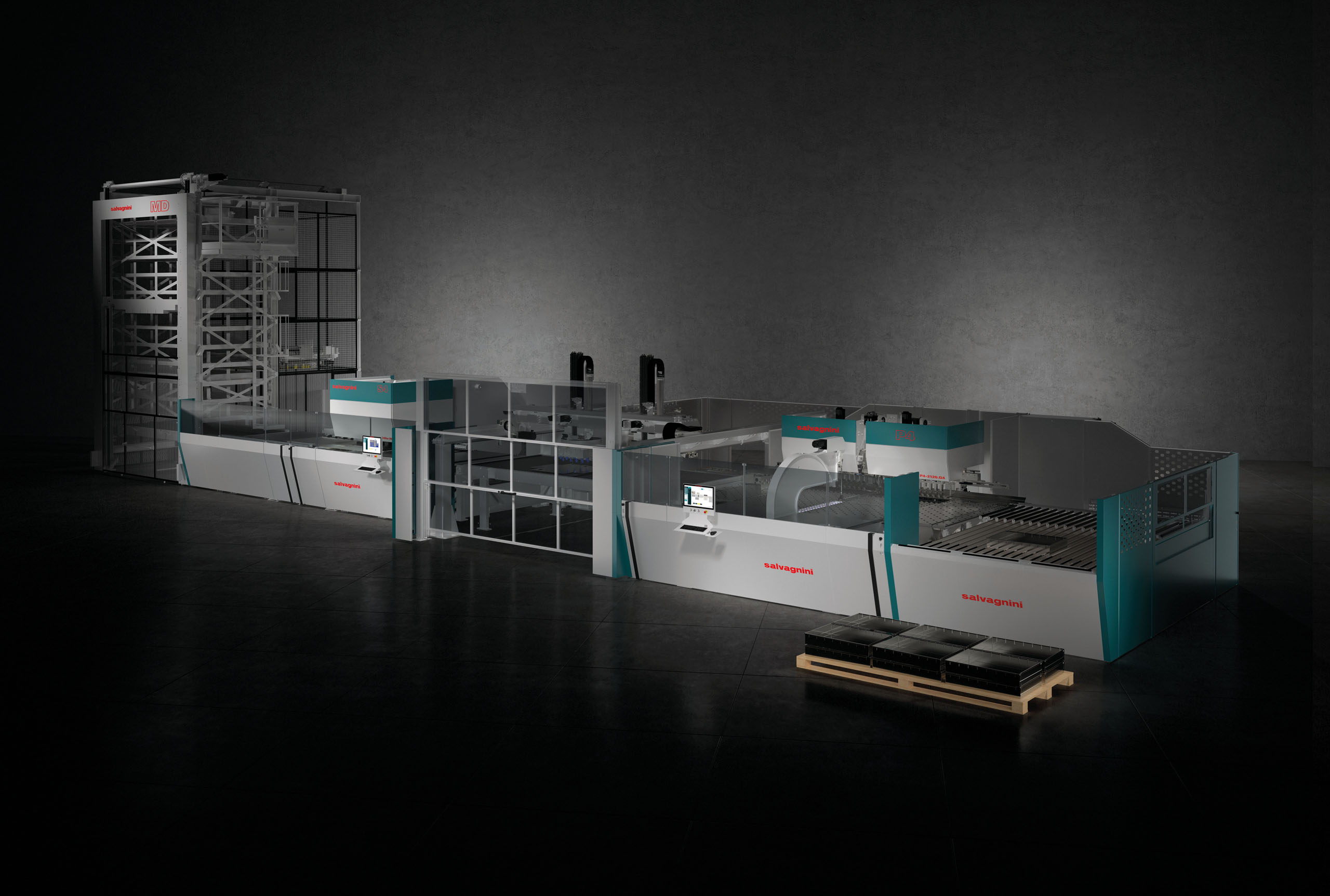
MAC3.0
MAC3.0은 절곡 중 소재의 인장강도를 측정하며, 생산 프로그램에 정의된 재질과 비교하여 그 편차를 보상할 수 있도록 절곡 사이클을 자동 조정합니다.
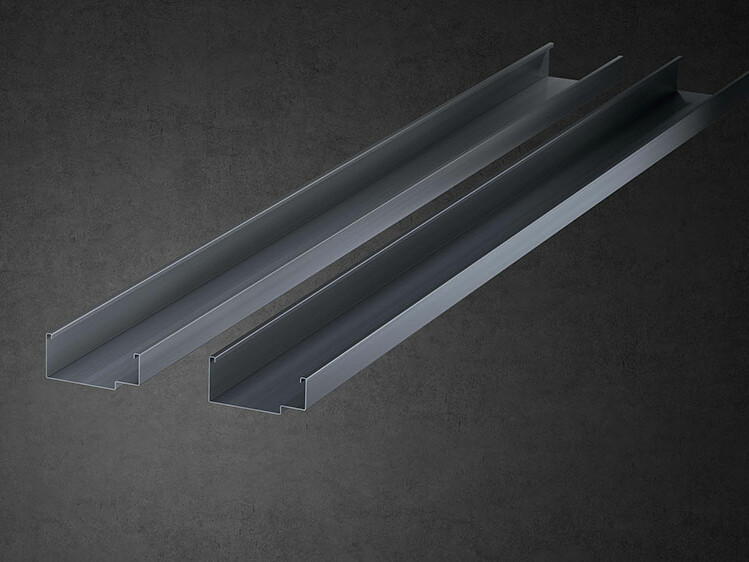
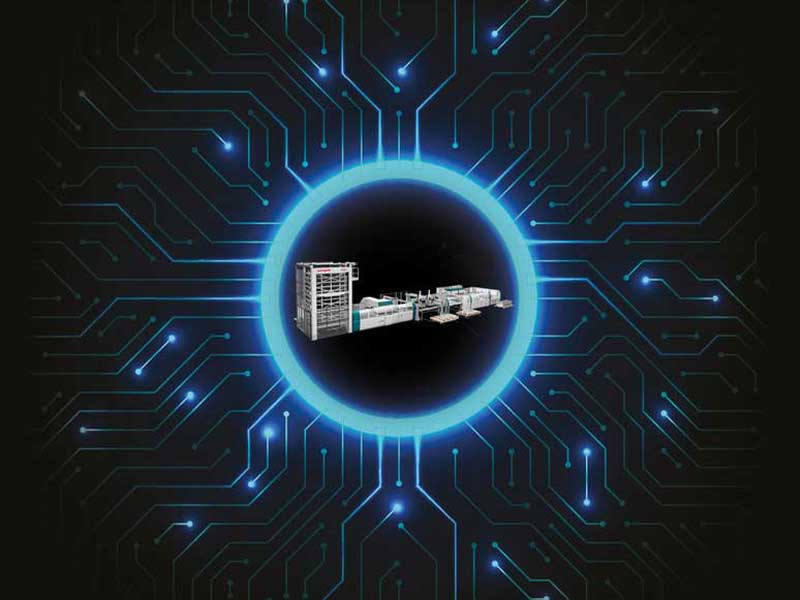
4차 산업혁명
디지털 전환과 인더스트리 4.0은 시장에서 경쟁력을 유지하기 위한 핵심적인 주제입니다. 이를 도입하면 고도로 자동화된 복잡한 통합형 고성능 시스템을 구현하고 관리할 수 있으며, 생산 레이아웃에 구조적 변화가 필요 없는 간단한 솔루션을 개발하도록 지원하므로, 스마트 제조의 세계에 훨씬 더 쉽게 접근할 수 있습니다.
궁금한 점이 있으신가요?