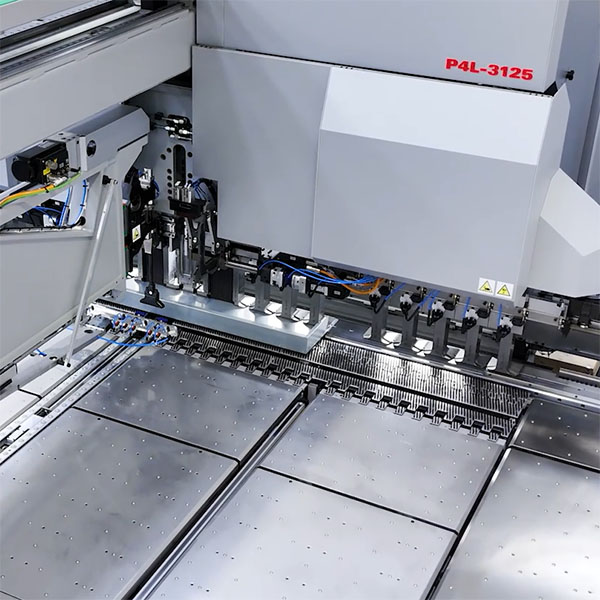
Insight
Tecnolaser: il servizio Rethinks per ridurre i tempi di produzione del 40%
Rethinks è il servizio Salvagnini che aiuta le aziende ad affrontare le sfide quotidiane imposte dal mercato ripensando e riprogettando la produzione per ottenere il massimo dagli impianti produttivi.
Rethinks significa ripensare, riprogettare, e mette la conoscenza e la competenza degli specialisti Salvagnini a disposizione dei clienti, per sfruttare al massimo il potenziale dei loro sistemi. Rethinks è la proposta ideale per chi vuole ottimizzare il processo di produzione di un prodotto migliorandone la qualità e l’efficienza, riducendo le fasi di lavoro, l’uso di materiale e i costi.
Di Rethinks fanno parte servizi diversi. Il primo servizio è un corso di design dedicato ai progettisti. Lavorare a monte per migliorare la conoscenza delle tecnologie a disposizione e delle loro potenzialità è il primo passo per efficientare il loro utilizzo. Il corso di design dota i progettisti di competenze avanzate.
Il secondo invece è un servizio di supporto alla progettazione. Gli specialisti Salvagnini mettono la propria esperienza e competenza a disposizione dei progettisti dei clienti, aiutandoli a progettare o riprogettare i propri prodotti. Si tratta di un vero e proprio supporto esperto nelle fasi operative di progettazione dei componenti che individua, caso per caso, le migliori soluzioni per garantire la riduzione degli sprechi e l’ottimizzazione dell'intero processo produttivo, anche a monte e a valle delle tecnologie Salvagnini.
Tecnolaser ha scelto Rethinks
Giulio De Bardi, Membro del Consiglio di Amministrazione di Tecnolaser, spiega quali sono i vantaggi derivanti dall’avere utilizzato il servizio Rethinks per il redesign di pannelli di carteratura macchine.
- Perchè riprogettare il prodotto?
"Spesso ci troviamo a realizzare cabinature di macchine dove sono presenti pannelli di varie forme e con varie dimensioni. Il vecchio processo produttivo che già attuavamo in azienda prevedeva il taglio laser di questi pannelli, la piegatura in pannellatrice che ha la versatilità per realizzare diverse dimensioni del raggio interno di piega, e poi la saldatura, che era il processo che ci serviva per andare a chiudere l'angolo del pannello e a ripristinare la finitura estetica. La nostra criticità era che questa lavorazione occupava molto tempo da parte dell'operatore, andando quindi anche a saturare capacità produttiva. Però richiedeva anche una certa manualità da parte dell'operatore, perché le lavorazioni di saldatura in continuo e di carteggiatura richiedono certe competenze e quindi avevamo la criticità che non tutti gli operatori a nostra disposizione potevano eseguire questo lavoro in maniera precisa e soddisfacente per il cliente. Chiaramente tutta questa attività manuale comporta anche un alto costo per il prodotto finito che noi andiamo a vendere al cliente." - Cosa è cambiato?
"Abbiamo modificato la sezione di taglio. Quindi mentre prima si aveva uno spigolo secco che veniva poi riportato in piegatura nella piega laterale che andava a generare un angolo di 90 gradi, siamo riusciti a riportare un piccolo lembo di lamiera che viene pannellato durante la piega raggiata e che quindi costituisce un supporto visibile che dà continuità al raggio di piega, mentre dall'altra parte l'operazione di saldatura è diventata molto più semplice, consentendo una saldatura a punti, non richiedendo più la carteggiatura e chiedendo anche meno skill da parte dell'operatore." - Quali sono stati i benefici?
"Questa nuova soluzione ci ha permesso quindi di andare ad abbattere i tempi di saldatura. Siamo riusciti a ottenere un risparmio nel processo del 40% che nella media delle nostre produzioni va a costituire un 15% sul costo del pannello finito. Oltretutto adesso abbiamo il vantaggio che non sono più necessarie particolari abilità manuali da parte dell'operatore nella rifinitura del pannello, nella molatura e nella ricostruzione del raggio di piega. Quindi tutti i nostri saldatori sono ora in grado di lavorare i pannelli ed eseguire le produzioni richieste."